See a list of where solar panels are assembled here.
See the latest coverage of the February 2018-initiated solar panel tariffs here.
When Suniva announced its shutdown earlier this year, many proclaimed the U.S.-manufactured panel industry as dead. “Not so fast,” said SolarWorld Americas, the largest U.S. crystalline-silicon solar manufacturer for the last 40 years, until its Germany parent company filed for insolvency one month later. The American division says it will still carry on with a few less employees, but the PR damage to the market had been tremendous.
Now add in the Suniva and SolarWorld-sponsored petition for trade tariffs on foreign panels. The petition asks the U.S. government to set a minimum price of 78 cents per watt on foreign panels, which is 17 cents more than the current average panel price in the United States. If the petition passes, SEIA estimates that the U.S. solar industry would lose 88,000 jobs—one-third of the current American solar workforce. The U.S. International Trade Commission (ITC) will make its decision on the case by Sept. 22, 2017, and developers, panel buyers and foreign panel manufacturers hold their breath in the meantime.
Just because two of the biggest U.S. panel manufacturers have hit some roadblocks doesn’t mean that the whole market is caving in. There are many companies waving the “Made in USA” banner and a few Canadian manufacturers ready to pick up the slack if “Made in North America” becomes the better default. Although many crystalline-silicon panel manufacturers operate as “boutique solar providers” (either in capacity size or through premium product), there are companies out there to fill domestic orders. And U.S. thin-film manufacturers are waiting on the sidelines to swing traditionally crystalline customers to their side.
Some U.S. and Canadian solar panel manufacturers described how things have changed in the six short months since Suniva’s exit, and they expressed whether they have the capacity or the desire to take on the need for U.S. and/or North American solar modules (all signs point to yes).
Solaria – Fremont, California
Solaria produces its PowerXT line of high-efficiency modules on assembly lines in Silicon Valley and also in Asia. The company announced in June that it plans to expand its California manufacturing capacity to more than 40 MW per year by the end of 2017, a decision that was not influenced by Suniva’s exit from the market.
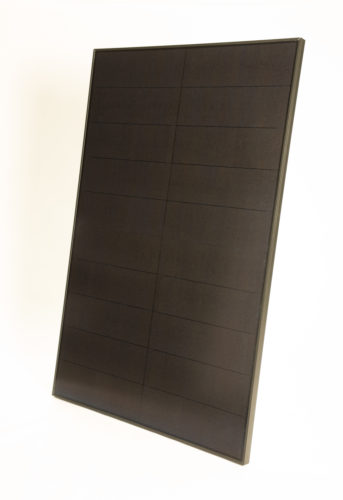
Solaria PowerXT module
“It was always Solaria’s intention to ramp up manufacturing in Silicon Valley,” said Solaria CEO Suvi Sharma. “Solaria has been—and remains—committed to the U.S. market.”
In total, Solaria should reach 100-MW capacity this year and will add more in 2018 to meet increased customer demand. This ramp-up has drawn more interest to the company.
“There are a number of distributors, installers and homeowners who’ve been interested in the fact that we’ve ramped up our manufacturing in the United States,” Sharma said. “Customers are extremely receptive and appreciative of the Solaria PowerXT modules, designed and produced with American innovation and ingenuity.”
Sharma said the trade case is a unique battleground in the United States. Solaria is invested in encouraging U.S. manufacturing and preventing international dominance, but at what cost?
“Accelerated global solar module manufacturing and innovation is vital to confronting the challenges posed by climate change,” Sharma said. “We’re keenly interested in boosting American PV manufacturing here at home, and that’s why we’ve ramped up our production capacity. Yet, we’re also concerned that placing tariffs on international imports could thwart the tremendous job growth we’ve been seeing in the U.S. solar sector.”
SolarTech Universal – Riviera Beach, Florida
SolarTech Universal manufactures 60-cell monocrystalline modules with Meyer Burger’s SmartWire Technology out of its primary facility in Southern Florida. The company, in production for two years, also has a PERC line and is working on black-on-black modules. SolarTech is open to the public and often gives tours of the facility, something that marketing associate Caty Weihl said increases interest in the newer brand.
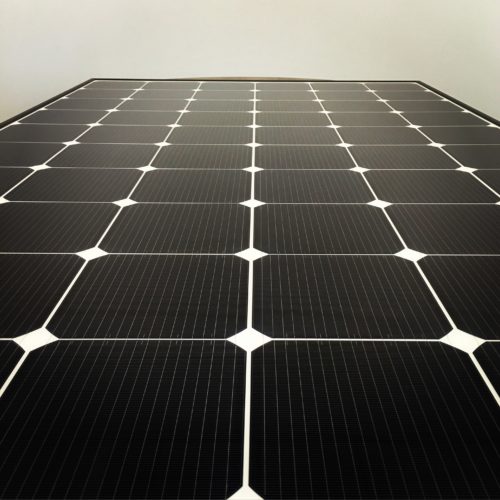
A SolarTech Universal solar panel
“We love giving tours of our facility so customers can see for themselves how much care we put into each panel,” she said. “It’s a level of service, transparency and value not found anywhere else.”
SolarTech has focused on producing a premium solar panel, more so than taking advantage of an open U.S. market.
“Our customers tend to be those with discreet tastes, who find value in premium, quality, U.S.-made products,” Weihl said. “We don’t have the same ‘race to the bottom’ mentality held by others in the industry. We keep our price competitive, but we also see the value in spending a little more on materials to show customers a lot more value.”
With those blinders on, SolarTech will continue to function as planned this year.
“We are very excited to get our new black-on-black module into production,” Weihl said. “We are planning to add additional shifts, creating dozens of jobs, to keep up with the demand. We are most proud of our ability to provide well-paying, highly skilled jobs in our community. The majority of our 40+ employees were hired from the surrounding area and specially trained to fill their position. Without the work they do, our product would not be what it is today. It is with them in mind that we strongly oppose additional tariffs to solar products.”
Silfab Solar – Mississauga, Ontario
Silfab Solar’s recently expanded 300-MW capacity production line in Ontario, Canada, may not make Made in USA panels, but executive advisor Geoffrey Atkins said the company’s North American modules are taking advantage of the open U.S. market.
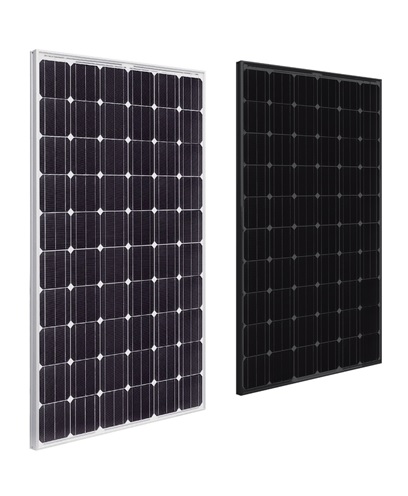
Silfab Solar modules
“There remains a strong market for customers seeking Made in North America quality for residential and commercial scale projects,” he said. “Customers are looking for the quality and service provided by North American-based manufacturers who can service and support their product and guarantee on-time delivery and consistent product availability.”
Silfab’s line of monocrystalline and bifacial modules has been in production for seven years, and that stability is well sought out right now.
“Silfab remains 100% focused on the North American premium quality market and delivering superior service and support for our products,” Atkins said. “Silfab operates a just-in-time business model and we continue to increase our manufacturing capacity to meet the needs of our North American customers and partners to ensure that they have a consistent supply of high quality modules at a competitive price.”
Seraphim Solar – Jackson, Mississippi
Seraphim Solar USA manufactures 300-W and 360-W modules out of its 160-MW capacity facility in Mississippi. The company announced in March that it has begun preparing for a 200-MW expansion to its annual capacity. Steve Ostrenga, Seraphim vice president of sales for the Americas, said the company’s message has stayed consistent: manufacturing high-efficiency modules without worrying about competitors’ missteps.
“Our industry has always and will continue to be turbulent, whether it be polysilicon shortages, anti-dumping/countervailing duties, price shocks due to oversupply or technological changes,” he said. “We recognize that the current situation is temporal. Our focus day-in, day-out is to build a great solar panel and service the customer.”
Seraphim got its start in 2015, and Ostrenga said it has residential, commercial and industrial customers eager for American modules. Seraphim has seen an uptick in inquiries since Suniva’s exit.
“Customers are revisiting their procurement strategies, identifying ways to mitigate supply chain risk and are thinking long-term versus spot purchasing,” Ostrenga said. “Our clients value Made in the USA manufacturing, our bankability through third-party insurance and solar financing partners, high-efficiency modules, quick turn-arounds and our dedication to service.”
Stion – Hattiesburg, Mississippi
Although Suniva and SolarWorld produce crystalline modules, the thin-film market is feeling the ripple effects of their struggles and the subsequent trade tariff petition. Stion produces frameless and framed thin-film CIGS modules in a 700,000-sq. ft manufacturing plant in Mississippi. Seth Stulgis, Stion director of marketing, said there has been increased interest from larger developers looking into Stion’s thin-film for future projects.
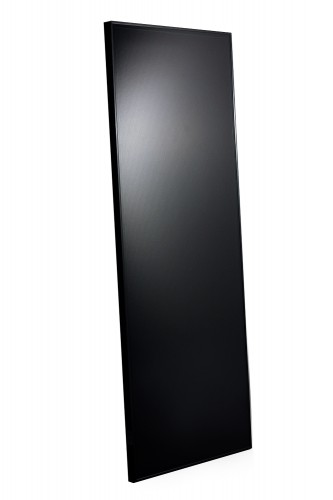
A Stion CIGS thin-film solar module
“Stion takes pride in being a 100% U.S. corporation,” Stulgis said. “We have seen an uptick in interest from developers looking to secure modules before year’s end due to the module shortage for U.S. clients as well as those looking to hedge against a potential minimum import price (MIP). Stion is both a thin-film module manufacturer and makes its modules in the United States, so it is not subject to an MIP.”
Some foreign module manufacturers are cutting back U.S. shipments because of the uncertainty around the trade case. Stion doesn’t have to worry about that and is in fact ramping up its production capacity to 150 MW each year at its Mississippi plant. The team is exploring technical initiatives to add capacity even faster.
“‘American-made’ is who we are and who we have always been,” Stulgis said.
*The photo originally with the Seraphim section was an incorrect image and has been removed and replaced.
suniva petition adds 17 cents more? try double. seia/gtm report the average current average price is 40 cents/watt in the us
Itek Energy in Bellingham, WA & Minnesota!
Hello can you please help me out Basically I looking for manufacturer of Latest technology in solar panel Quantum Dot solar cell ,
If you can provide with the names and telephone number will be appreciated,
Regards
Majid
I don’t recommend quantum. Theses module has deficit in the design, and the data on spec sheet is not correct.
I would like to make 2 points. What is our recourse as Solar Developers for damages to our business. We had to lay off 10 people already because the complaint impacted module supply causing a delay in project closings impacting revenues. If module prices are increased because of this it will ruin the project economics on millions of dollars of contracts. Can we sue for damages? How about dangling a big class action lawsuit in front of Suniva for damages? Maybe then they would withdraw the complaint. There has to be severe repercussions.
Secondly, we have done work for local governments who request the use of American made components for their projects and we have been able to submit competitive bids using American products.
You have stated some very good points! Some local governments set basic requirements and we set out to meet those requirements only to have indirect actions taken that can cause issues. I will look to add a clause in future contracts to address the issue so it does not derail the deal. Solar is an investment and we need to think of it that way so there are risks but we want to keep everyone positive and looking at the big picture.
Auxin Solar in San Jose?
I was thinking of that one, too, Brandon.
Did not forget about them! We recently did an extended feature on Auxin: https://www.solarpowerworldonline.com/2017/07/qa-california-based-solar-panel-manufacturer-auxin-solar/
You didn’t mention Global Solar Energy in Tucson, AZ. The largest manufacturer of flexible CIG thin film pv panels in the US.
Don’t forget the big solar installation in the rooftop at Solartech Universal, it a good example how a company can save energy. Solartech Universal is talking with the example!!
Don’t forget about Mission Solar Energy, San Antonio, Texas. Their panels have been mostly used in utility projects, but they look great on a residential roof as well.
Yup there panel really look good on rooftop